Olefin fibers have great bulk and cover
while having low specific gravity. This means “warmth without
the weight.”[1]
The fibers have low moisture absorption, but they can wick
moisture and dry quickly.[2]
Olefin is abrasion, stain, sunlight, fire, and chemical
resistant. It does not dye well, but has the advantage of being
colorfast. Since Olefin has a low melting point, textiles can be
thermally bonded. The fibers have the lowest static of all
manufactured fibers and a medium luster. One of the most
important properties of olefin is its strength. It keeps its
strength in wet or dry conditions and is very resilient. The
fiber can be produced for strength of different properties.
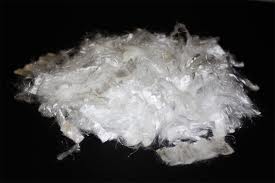
Basic Principles of Olefin Fiber Production — Olefin fibers
(polypropylene and polyethylene) are products of the polymerization
of propylene and ethylene gases. For the products to be of use as
fibers, polymerization must be carried out under controlled
conditions with special catalysts that give chains with few
branches. Olefin fibers are characterized by their resistance to
moisture and chemicals. Of the two, polypropylene is the more
favored for general textile applications because of its higher
melting point; and the use of polypropylene has progressed rapidly
since its introduction. The fibers resist dyeing, so colored olefin
fibers are produced by adding dye directly to the polymer prior to
or during melt spinning. A range of characteristics can be imparted
to olefin fibers with additives, variations in the polymer, and by
use of different process conditions.